Introduction
In order to produce goods and services of any type, a business needs raw materials and equipment. The process through which businesses acquire their various needs is called the supply chain.
If you’re a business owner, you know that supply chain operations go beyond simply buying raw materials; this process involves figuring out what you need, when you need it, how much you currently need or will need in the future, how long your current stock will last, when you should begin to make a new batch, how long it will take the needed materials to get to you, how long in advance you should place an order, who offers the highest quality of what you need, what is the cheapest possible price and if there any suitable alternatives.
What is Supply Chain Operations?
Supply chain operations includes every process that aids in either the management of the flow of goods and services, or the transformation of raw materials into finished goods. Ideal supply chain operations help you to maintain efficiency in your business, lower costs, improve product quality, strengthen customer and supplier relationships, enable you to keep up with demand, and so much more.
Supply chain operations can be broken down into six phases, the first of which is procurement. We covered this phase of supply chain operations in our article series on improving procurement. Next comes the material management phase.
What is Material Management?
Material management is a core supply chain function that is concerned with planning, organizing and controlling the flow of materials from their initial purchase through internal operations to their introduction into the manufacturing process.
The fundamental objective of the material management functions is the acquisition of materials and services of the right quality, in the right quantity, at the right time, from the right source and at the right price. It begins with the receiving and inspection of materials and ends with the issuance of the material to production to meet up with the customer’s demand as scheduled and at the lowest cost.
Inventory management and control goes hand in hand with material management because it helps keep track of raw material and specific products, which in turn minimizes costs to the organization and ensures maximum return on working capital.
In this article, we’ll discuss inventory optimization and how you can not only improve your process effectiveness, but also improve the material management phase of your business’s supply chain operations.
Optimize your inventory and your entire supply chain with well-written OKRs. Try the Profit.co OKR Management platform for free today!
The Importance of Inventory Optimization
In today’s business environment, companies are looking at being profitable at the earliest opportunity. To achieve this objective, organizational expenses have to be controlled along with increased revenue flow. Since inventory management takes considerable expense, it is vital to optimize its effectiveness. Inefficient inventory management cost the global economy more than $1.1 trillion in 2015.
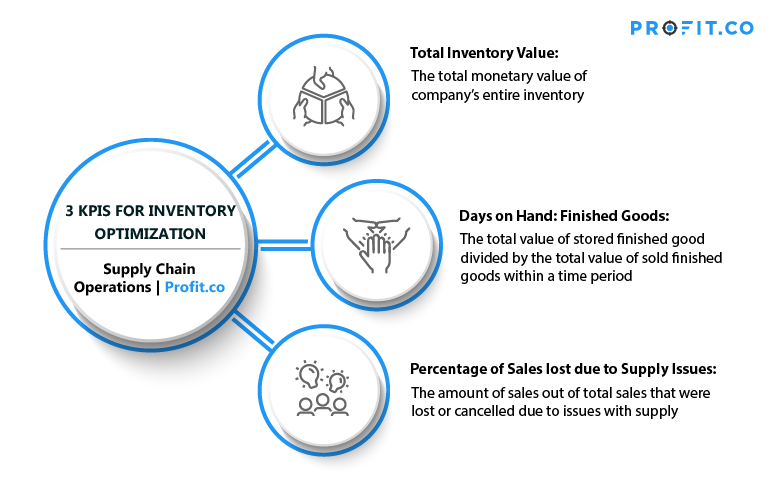
A high Total Inventory Value metric which is the total monetary value of a company’s inventory can be a considerable expense to the company, while low figures for Days on Hand: Finished Goods metric, which refers to the total value of stored finished goods divided by the total value of sold finished goods within a time period, can make it hard to fulfill customer demand.
This could in turn increase the metric of Percentage of Sales lost due to Supply Issues. This issue affects a third of all businesses. Statistics for June 2020 also show that the average retail business has $1.37 worth of inventory for every $1 worth of sales showing overstocking of inventory.
Improvement should start with determining the state of the firm’s inventory management process. Then, a structured approach to inventory planning and control can help manufacturers maintain a high customer service level while also reducing variable costs.
5 Steps to Improve Inventory Planning and Control Process
We recommend a five-step structured approach to improve your inventory planning and control process, as follows:
1. Assess inventory operations
The first step is a thorough examination of the inventory management process in order to determine its state. Identify and discuss with each stakeholder their roles in the process, obstacles they face and what improvements can be made to make their job more effective. Study the interworking relationship between different units in the process and see if there is clarity of roles or an overlapping of responsibilities.
The findings from this exercise should be documented. The documents should be able to reveal operational deficiencies, based on metrics like Planned vs. Actual Shelf Life (which measures the percentage difference in the planned storage duration and the actual storage duration of the company’s inventory). These deficiencies should be ranked by their impact on the process, and improvements recommended. Statistics show that inventory for retail business is only accurate 63% of the time.
Comparing the firm’s inventory practices against those of the industry leaders through a third party will be useful for assessment. Communicate to all stakeholders the assessment findings and proposed improvement plans so they can be engaged in the improvement process.
2. Develop an inventory management plan
The assessment findings should be turned into an action plan. The Ideal inventory management plan should be able to lower the Carrying Cost of Inventory metric, which is the expenses incurred on storing inventory and its shipping, and ensure good Total Inventory Value metric which can withstand supply chain or production fluctuations. Statistics have shown an average reduction of 10% in the Carrying Cost of Inventory metric when Inventory management is improved.
Segmentation of inventory into raw materials, work-in-process and finished goods is necessary. Each category should be further segmented based on different classification criteria. A good action plan should have individual plans for each of these sub-segments, which are then combined to create an overall inventory plan. This plan should include optimizing the Average Warehouse Capacity Used by storing fast-selling goods in an easily accessible position in the warehouse. This action will improve the Average Shelf Life metric and keep their Cycle Time: Internal Order Customer Processing KPI at a low rate.
There should be quality control standards for the inventory management process along with operational definitions, especially if the company was involved in a merger or acquisition, which brings along different criteria. The first step here is addressing operational shortfalls. Taking care of these limitations might take time, so an intermediate plan that will meet inventory objectives in the face of these drawbacks is necessary. Once these assets like technology systems are made available, the full project can be implemented.
The plan should also include action plans to reduce the Obsolete Inventory Maintenance metric, which is an indicator of the presence of obsolete products in storage. This should include setting up a cross-functional team that can come up with innovative ways of disposing of these items. One way could be conducting heavily discounted sales of such items, so they do not add to the Carrying Cost of Inventory metric.
3. Put the plan into action
Executing the plan should be the next step. Monitoring of the inventory process and maintaining laid down quality control standards is crucial to its success. Management has to approve any exceptions from the plan only when necessary. There should be open communication and collaboration between all stakeholders in the inventory process, including suppliers.
The inventory management system should include a process that reviews stakeholder performance, especially suppliers, since the quality of the raw materials they supply can impact the Acceptance Rates of Finished Goods metric of the firm. The role of each unit in the inventory process should be clarified and responsibilities apportioned. Standardization of the inventory management system is necessary so that it is easy to execute, and tasks can be easily delegated.
4. Measure the performance against the plan
This is necessary to sustain improvements, as organizations cannot improve what they do not measure. Any action in the inventory process against the laid down plan should be investigated and corrected immediately. There should be a high level of inventory audits to ensure that effectiveness is maintained.
Also, there should be specific key performance metrics and Key Performance Indicators (KPIs) for evaluating performances of each stakeholder and the firm. For employees, these productivity metrics should include Cycle Times for Dock-to-Stock; the amount of time needed to store received goods from when it is received, Material Stocking; the time duration between receiving supplies and storing them in the warehouse, Component Picking; the time duration between the start of gathering components for the production of a customer’s order and its collation, Lines Received and Put Away per Receiving Employee; the average amount of time an employee uses to process an order line, and Supplier Orders Processed per Receiving Employee; the average amount of orders processed by individual employees.
Identifying high and low performing suppliers should be according to performance metrics that include the Cycle Time: Supplier Order Delivery; the amount of days between making a supply order and its delivery, Undamaged Supplier Shipment Rate; the percentage of total supplies received in an undamaged state, Materials Acceptance Rate; the percentage of materials supplies approved for use by quality control on the first pass, and the Supplier Order Documentation Accuracy Rate; the number of supplies with accurate documentation as a percentage of total supplies. Results of the metrics should result in appropriate actions.
There should also be planner metrics to measure the firm’s inventory effectiveness, some of these metrics include Carrying Cost of Inventory as percentages of Total Inventory Value; the percentage of the total value of inventory used on storing and shipping it, COGs (Cost of Goods); the percentage of the total costs of goods used on inventory storage and shipping expenses, and Sales metric which is the inventory storage and shipping expenses as a percentage of the sales value.
5. Ensure Improvement is Continuous
Opportunities to make the inventory process better should be sought to maintain its effectiveness and make it robust enough to meet unexpected emergencies like supply chain disruptions. Actions here should include constant review of the process, improving data analytics to ensure optimizing Just-in-Time delivery metric and minimize minimum stock orders. Other actions should be investigating deviations from laid down processes and codifying the solutions, improving employee operational knowledge, carrying out operational improvement schemes with suppliers, and lowering cycle and lead times in various areas.
Final Thoughts
Improving processes through the material management phase of your supply chain operations can have a large impact on the overall efficiency and effectiveness of your organization.
Optimizing the flow of your inventory operations will help you keep better track of important trends in your inventory and leave you better prepared to manage this and more aspects of the material management phase of your supply chain.