What is a Balanced Scorecard?
According to Gartner, “A balanced scorecard (BSC) is a performance measurement and management approach that recognizes that financial measures by themselves are not sufficient and that an enterprise needs a more holistic, balanced set of measures that reflects the different drivers that contribute to superior performance and the achievement of the enterprise’s strategic goals.”
The Balanced Scorecard, developed by Robert S. Kaplan and David P. Norton in the early 1990s, extends beyond traditional financial metrics to include perspectives such as customer, internal processes, learning, and growth.
These perspectives include:
- Financial
This dimension evaluates the organization’s financial stability alongside the effectiveness of its mission-driven activities. - Employee
It examines the overall health of the organization, including employee engagement, skills, and growth opportunities. - Customer
This area focuses on the relationships with and satisfaction of those who support or benefit from the organization’s products and services. - Operations
This evaluates the efficiency of the organization’s internal processes and infrastructure.
“A mere 7% of employees today fully understand their company’s business strategies and what’s expected of them in order to help achieve company goals.”
The essence of the balanced scorecard lies in its ability to foster excellence across these crucial areas, which is vital for achieving overarching operational excellence. An organization that neglects any of these areas risks compromising its performance. For instance, a non-profit overly concentrated on donor/customer aspects may diminish its program’s effectiveness, while a business overly fixated on short-term earnings per share might undermine long-term value for shareholders. In essence, optimal management of an organization’s comprehensive resources demands equal attention to these four elements.
Ready to unlock how our innovative solutions can propel your manufacturing goals to new heights?
The Essence of the Balanced Scorecard in Manufacturing
In the context of manufacturing, the multidimensional approach of the BSC ensures that companies don’t just focus on cutting costs or improving production times but also on enhancing quality, innovation, and customer satisfaction.
Strategic Alignment and Focus
One of the primary benefits of implementing a BSC in manufacturing is aligning operational activities with the organization’s strategic vision. The BSC ensures that everyone is working towards the same outcomes by translating lofty strategic goals into specific, actionable objectives across different departments. This alignment is crucial in manufacturing, where siloed operations can often lead to inefficiencies and wasted resources.
Driving Performance with Key Metrics
The BSC encourages using Key Performance Indicators (KPIs) tailored to the manufacturing sector, such as Overall Equipment Effectiveness (OEE), cycle times, defect rates, and customer return rates. These metrics offer a clear, quantifiable measure of performance across the four perspectives of the BSC, allowing manufacturers to track progress, identify areas for improvement, and make data-driven decisions.
Enhancing Quality and Customer Satisfaction
Quality and customer satisfaction are paramount in manufacturing. The BSC framework places a strong emphasis on understanding and meeting customer needs, encouraging manufacturers to adopt a customer-centric approach. By integrating customer feedback into the strategic planning process, manufacturers can continuously improve product quality and customer service, leading to higher customer satisfaction and loyalty.
Fostering Innovation and Continuous Improvement
The learning and growth perspective of the BSC highlights the importance of employee training, knowledge management, and technological innovation. In the competitive manufacturing sector, continuous improvement and innovation are key to maintaining a competitive edge. The BSC framework supports this by setting objectives that promote research and development, process improvement, and skill development among employees.
Essential Steps to Implement Balanced Scorecard in the Manufacturing Industry
Implementing a BSC in a manufacturing environment requires a structured approach, starting with a clear understanding of the company’s vision and strategic goals. The next step involves identifying the specific metrics that will be used to measure performance in each of the four areas. These metrics should be carefully selected to ensure they are relevant, measurable, and capable of driving meaningful change. Regular reviews and updates to the BSC are essential to reflect changing market conditions, strategic shifts, or improvements in technology.
The above-listed essence of balance score helps you understand the nuances that one needs to identify before implementing. Understanding the process at its full potential will help you achieve your goals related to your manufacturing unit.
So before implementing it, make sure you learn its functionalities.
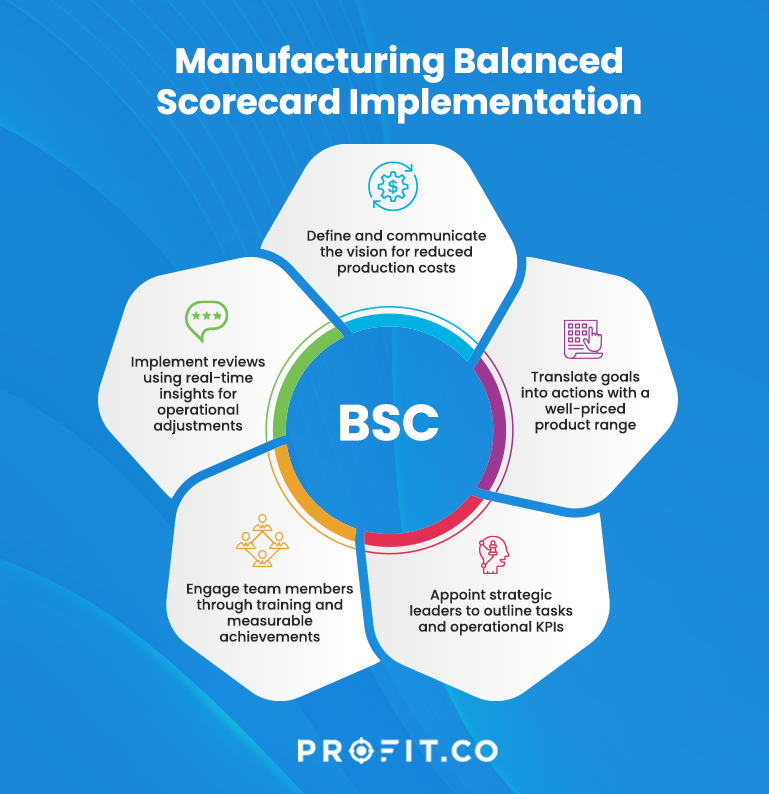
- Define and Communicate Vision and Goals: Clearly articulate the organization’s vision, mission, and desired outcomes. It’s vital to reach a consensus on these foundational elements.
- Translate Goals into Action: Transform the mission and desired outcomes into specific strategic objectives and actionable operational goals.
- Designate Strategic Leadership: Appoint a dedicated executive to manage each segment of the strategic plan. This leader will detail the tasks and key performance indicators (KPIs) tied to every operational goal.
- Engage All Team Members: Ensure each individual within the organization links their personal work plans and measurable achievements to the defined operational goals.
- Implement a Continuous Review System: Create a mechanism for regular assessment of performance metrics by both executives and the broader organization. Use this data to iteratively refine the strategic direction as needed, leveraging real-time insights.
This approach ensures the strategic alignment of manufacturing operations and fosters an environment of continuous improvement and operational excellence.
The BSC in manufacturing is pivotal for optimizing production efficiency, quality management, financial performance, and workforce development. It’s designed to tackle industry-specific challenges, including operational efficiency, product quality, cost reduction, and innovation.
Consider a leading manufacturing company struggling to synchronize production processes, manage costs effectively, and maintain product quality in a highly competitive market. Despite efforts to enhance performance, the absence of a cohesive strategy and measurable goals resulted in inconsistent outcomes and missed opportunities.
The solution lies in adopting the BSC framework tailored to meet the distinctive needs of the manufacturing sector.
Start your BSC journey in manufacturing today
The BSC framework for the Manufacturing Company was customized to include
Perspective | Objective | Key Results | Initiatives |
---|---|---|---|
Financial | Optimize cost structure | 10% reduction in production costs | Implement cost-effective procurement strategies |
– | Increase revenue by 15% from new markets | Diversify product range and enter new markets | |
Customer Satisfaction | Enhance product quality | 20% reduction in defects rate | Adopt Total Quality Management (TQM) practices |
Improve delivery times | Decrease lead times by 15% | Streamline logistics and supply chain processes | |
Internal Processes | Boost production efficiency | 10% increase in output per hour | Implement lean manufacturing techniques |
Foster innovation | Launch 5 new products annually | Establish a cross-functional innovation team | |
Learning and Growth | Develop workforce skills | 25% staff participation in skill development programs | Launch targeted training and development programs |
Implement advanced manufacturing technologies | 30% increase in automation levels | Invest in state-of-the-art machinery and software |
Positive Outcomes
- Achieved significant cost reductions while enhancing revenue streams.
- Improved product quality and customer satisfaction, leading to better market competitiveness.
- Increased efficiency and reduced lead times through streamlined processes.
- Elevated staff expertise and embraced technological advancements, boosting innovation.
Challenges
- Resistance to change among staff and management.
- Integrating new technologies with existing systems.
- Maintaining consistency in product quality during the transition.
Overcoming Common Challenges
Transitioning to a BSC framework involves navigating obstacles such as change resistance and technological integration. Successful implementation requires clear communication of benefits, comprehensive training, and phased technology adoption. Utilizing software solutions that simplify data analysis and performance tracking can mitigate these challenges, making the BSC more manageable and impactful.
Leveraging Technology
The advent of Industry 4.0 technologies offers immense opportunities to enrich the BSC framework in manufacturing. IoT devices, AI, and real-time data analytics can provide deeper insights into operational efficiencies and quality control, while ERP systems enhance visibility across the production lifecycle. This synergy simplifies BSC implementation and elevates data quality and strategic decision-making.
A Strategic Blueprint for Manufacturing Excellence
The BSC, complemented by Objectives and Key Results (OKRs), equips manufacturing organizations to navigate the complexities of modern production challenges. Integrating BSC and OKRs effectively requires a clear understanding of how both frameworks complement each other. We start by aligning OKRs with the four perspectives of the BSC to ensure comprehensive coverage of strategic objectives. Regular cross-functional meetings are held to review progress and ensure alignment. We also use technology tools to track and visualize progress on OKRs and BSC metrics, facilitating real-time adjustments and fostering a culture of continuous improvement. This integrated approach enhances strategy execution by ensuring that all levels of the organization are working towards common goals with clear metrics and accountability
Final Thoughts
The Balanced Scorecard offers a powerful framework for manufacturing companies seeking to navigate the complexities of modern production environments. By focusing on a balanced set of financial and non-financial metrics, the BSC helps manufacturers align their operations with strategic objectives, drive performance improvement, and achieve long-term success. As the manufacturing sector continues to evolve, the principles of the BSC remain as relevant as ever, providing a roadmap for continuous improvement and competitive advantage.
Dive into the future of manufacturing excellence with Profit.co!
Related Articles
-
Burn, Turn, Churn: Will your business end up in an urn?
Urns are traditionally used to store the ashes of the deceased after cremation symbolizing the end of a person’s journey.... Read more
-
How does transparency in planning, processes, and people directly drive business success?
Transparency isn’t a buzzword. It’s a game-changer. When businesses keep transparency as the foundational building block across the c, processes,... Read more
-
Are You Tolerating Too Much Crap?
The business world is undergoing a massive shift with the rise of AI. Change is happening at an unprecedented pace,... Read more
-
How to Use Benchmarking and Stay Ahead of the Competition
Benchmarking is an excellent and efficient way to discover your business's highest performance standards by examining other companies’ success. As... Read more